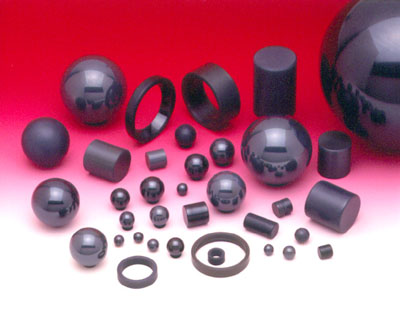
Novedades industriales en EMO 2003
Novedades industriales en EMO 2003
Comunicate con el proveedor:
!noticia guardada!
Saint-Gobain Advanced
Ceramics demostrará los beneficios de las esferas cerámicas
Los visitantes de EMO Milán
podrán apreciar los beneficios de las aplicaciones de las esferas cerámicas
Cerbec, especialmente en rodamientos, para disminuir los costos totales de operación
en productos industriales.
Además de una exhibición de la compañía y de sus productos, varios clientes de Cerbec presentarán algunas de sus aplicaciones. De acuerdo con el fabricante Saint-Gobain Advanced Ceramics, las esferas Cerbec duran más y proporcionan mejor desempeño en rodamientos que las esferas de acero, debido a su baja expansión térmica, superficie más lisa, alta dureza, elevada resistencia, menor peso y superior resistencia a la corrosión eléctrica. Varias demostraciones de estas características serán presentadas en el stand de Saint-Gobain.
Rodamientos, guías lineales, dispositivos médicos y dentales, equipos de procesamiento de semiconductores, husillos, hornos, instrumentos aeroespaciales, robótica, motores eléctricos, herramientas eléctricas, maquinaria para fabricación de papel y tornillos de bolas recirculantes son algunas de las muchas aplicaciones de las esferas cerámicas en actuadores, manejadores y procesos de automatización.
EdgeCAM versión
8 incrementa la velocidad de rotación del eje B y del subhusillo
Pathtrace Systems introduce
técnicas avanzadas en la rotación del eje B y el subhusillo y
automatiza la programación CAM para el fresado de bolsillos en EdgeCAM
Versión 8.
Las dos nuevas características incorporadas en las últimas versiones de EdgeCAM se basan en tecnología y programación ya probadas.
"Los avances de EdgeCAM automatizan altamente los procesos CAM (explica Steve Sivitter, CEO de Pathtrace para las Américas). Con el nuevo selector automático de herramientas en su centro, EdgeCAM Strategy Manager ahora incluye fresado de bolsillos y toma decisiones ´al vuelo´ con base en variables del proceso, tales como material, herramienta de corte, máquina-herramienta y geometría de la pieza.
"Las características en la rotación del eje B y el subhusillo ayudan a los usuarios a aprovechar la nueva línea de máquinas rotatorias multieje y multihusillo. El objetivo de las nuevas características es simplificar la programación de estas costosas y complicadas máquinas y mejorar la calidad de los programas en sí. Al mismo tiempo, el EdgeCAM V8 simula estas operaciones de tal forma que los programadores pueden balancear y sincronizar los ciclos, manteniendo una alta utilización de máquina", agraga Sivitter. La versión 8 del EdgeCAM será presentada en el stand de ProCAM Sistemi de Padua, el distribuidor Italiano de Pathtrace.
Nuevas torretas,
plataformas y módulos proveen sujeción de piezas con alta precisión
y repetibilidad
Alta densidad, elevada
precisión y versatilidad en acomodar diferentes tamaños de piezas
son beneficios de los nuevos estándares de Kurt Manufacturing: torretas
SeraLock, plataformas y módulos para sujeción de piezas WedgeLock.
Este nuevo sistema de sujeción con módulos autoalineantes permite crear accesorios equivalentes a los fabricados a la medida del cliente en menos tiempo del que toma el diseño de uno de estos. La sujeción con SeraLock hace posible el mecanizado de piezas semejantes y diferentes en el mismo montaje. Este sistema utiliza componentes reutilizables para sujeción, que pueden ser combinados y acoplados para sujetar piezas de cualquier tamaño.
Diseñados para alcanzar alta densidad y gran repetibilidad en sujeción de piezas, las torretas y plataformas SeraLock son diseñadas con superficies aserradas en forma de V para el alineamiento preciso y repetible de los módulos de sujeción WedgeLock.
Las superficies de montaje de SeraLock permiten una rápida y repetible precisión cuando se reposicionan elementos de sujeción como los de WedgeLock. Estos se alinean y ajustan con precisión y rapidez, lo cual es un requerimiento en el competido mundo de la manufactura actual. Debido a la versatilidad del sistema de SeraLock, los montajes con un rango que va desde cargas de alta densidad de piezas pequeñas hasta configuraciones de una sola estación para piezas muy grandes, pueden ser acomodados sobre la misma superficie de soporte.
Las torretas SeraLock están disponibles en modelos de uno, dos y cuatro lados, con una base que se puede montar en un centro de mecanizado horizontal o en una mesa rotatoria en un centro de mecanizado vertical. Hay tamaños disponibles para la mayoría de los centros de mecanizado. También se diseñan sistemas a la medida del cliente.
Nuevas herramientas
para abisagrar
Con las nuevas herramientas
para abisagrar de Mate Precision Tooling se pueden fabricar nudillos de bisagras
en piezas metálicas y otros productos similares, con la precisión
de una prensa punzonadora CNC. La incorporación de bisagras directamente
en estos productos, evita los componentes externos de las bisagras y su ensamblaje.
El nuevo herramental de Mate, para abisagrar, es diseñado con una herramienta superior rugosa de un solo cuerpo y un ensamblaje inferior que permite retirar la base de la herramienta. El diseño de esta herramienta produce formas de nudillos limpiamente contorneados, incluidos nudillos múltiples, sin ningún esfuerzo para los componentes de la herramienta. Esto alarga la vida de la herramienta, pues evita el desgaste prematuro y la necesidad de mantenimiento.
La operación de la herramienta es simple. Los nudillos son formados a partir de una lámina plana prepunzonada usando dos herramientas y tres golpes (en el primer golpe, la herramienta 1 genera el radio al final del nudillo; en el segundo golpe, la herramienta 1 genera el radio al inicio del nudillo, y con el tercer golpe, la herramienta 2 curva la forma para completar el nudillo).
Los nudillos se pueden fabricar en acero suave, aluminio y acero inoxidable en un rango de espesores desde 0,030" (0,80 mm) hasta 0,060" (1,50 mm), incorporando pasadores de diámetros desde 0,062" (1,60 mm) hasta 0,188" (4,77 mm).
Además de la caja de control electrónico, Mate Finge Tooling es ideal para fabricar bisagras en instrumentos, calefactores, aire acondicionado, estufas, hervidores y componentes similares.
Las herramientas para abisagrar de Mate se fabrican en acero de larga vida mediante electroerosionado y técnicas de fresado duro. Esto permite mecanizar con alta precisión la geometría de la herramienta requerida para producir la forma directamente sobre el blanco sólido endurecido. Fácil de instalar, la herramienta para abisagrar de Mate suministra una alta calidad en la pieza con completa confiabilidad en la operación.
Las herramientas para abisagrar se encuentran disponibles para la mayoría de las prensas de punzonado, como las de Amada, Euromac, Finn-Power, Murata Wiedemann, Trumpf y todas las máquinas de torreta gruesa. El equipo de ingeniería de Mate suministra una evaluación gratuita de cada aplicación de herramienta para abisagrar como parte del proceso de cotización.
SolidWorks 2003 disminuye
el tiempo de diseño y aumenta la precisión
SolidWorks Corporation introdujo SolidWorks 2003, la última versión
de su programa para diseño asistido por computador en tres dimensiones
(CAD 3D) que hace más eficiente el diseño y les permite a las
compañías introducir sus productos en el mercado más rápidamente.
SolidWorks 2003 presenta cientos de nuevas mejoras que ayudan a los usuarios a analizar la integridad estructural de sus diseños, transmitir información sobre sus diseños con otros usuarios, localizar catálogos de proveedores de piezas que se pueden bajar por internet y acelerar el proceso de diseño con nuevas herramientas de modelado. Estas nuevas características hacen que los ingenieros y diseñadores sean más productivos y que las compañías ofrezcan más competitividad en su mercado.
Las herramientas de análisis de SolidWorks 2003 les permiten a los diseñadores e ingenieros obtener diseños acertados al primer intento, economizando el tiempo y el costo de reparar errores durante la producción. SolidWorks 2003 también le ofrece al usuario la flexibilidad de importar y trabajar con una variedad de formatos de archivos, incluidos AutoCAD y CADKey. Esta característica ayuda a los usuarios a adoptar el 3D e integrar diseños de terceras partes en sus archivos CAD, para así poder terminar rápidamente sus diseños. El SolidWorks 2003 también es el primer programa CAD 3D convencional que les permite a los usuarios simular de manera real el movimiento, de tal forma que se puede revisar fácilmente el funcionamiento de los engranajes en operación e identificar cualquier error en el diseño antes de manufacturar.
"Ahora podemos arrastrar y pegar piezas de nuestros sistemas de ingeniería inversa en SolidWorks, en lugar de tener que convertir archivos manualmente. Esta característica no sólo nos ahorra una significativa cantidad de tiempo y trabajo sino que también nos da la oportunidad de obtener archivos con alto contenido de color y texturas en el proceso de diseño", afirma Brian Lothson, ingeniero de desarrollo de Alloyd.
Studer en la feria
La empresa suiza fabricante
de máquinas rectificadoras presentará varias de sus nuevas máquinas
en la feria italiana. Entre sus novedades se encuentra el rectificado de alta
velocidad de su máquina S32, que muestra cómo el tiempo de rectificado
se puede reducir en 30% o 40% en piezas grandes y medianas. Esto se consigue
con velocidades de rectificado de hasta 125 m/s y con la ayuda de sistemas de
control inteligente que pueden generar rápidos cambios en el tiempo.
Otro aspecto importante es la introducción de la nueva máquina S33 de rectificado cilíndrico universal, basada en la exitosa serie Eco, pero que incluye innovaciones tales como rectificado de interiores y cobertura completa de la máquina. El precio de introducción de la S33, desde abril de 2003, siempre ha llamado la atención de clientes y competidores.
Mediante el constante refinamiento de los programas de rectificado de interiores, Studer ofrece soluciones para la mayoría de las aplicaciones de rectificado. El nuevo modelo S120 ha sido diseñado para producción masiva de pequeñas piezas. Los modelos S140/S140 están diseñados para trabajos de alta producción en la industria automotriz. Para el rectificado de interiores, se encuentra el modelo S145, usado en la industria de la aviación, como en el caso de la manufactura de componentes para el Airbus.
Durante la EMO se explicarán temas relacionados con operadores de máquinas y gerencia. Se incluirán ejemplos en el uso de programas CAD y otros programas de Studer tales como StuderGrind y StuderVirtual.
El StuderGrind ayuda a encontrar el método más económico de rectificar una pieza y determinar de manera sencilla el mejor método de rectificado, el precio y la forma de entrega. El StuderGrind facilita la visualización de la geometría del disco de rectificado, el montaje y el programa de la pieza, por lo cual simplifica la puesta a punto de la máquina. El operador de la máquina recibe los datos y los planos de la pieza y puede poner a punto la máquina en poco tiempo. También se evitan las colisiones mediante la simulación de los programas en el PC.
El programa StuderVirtual fue diseñado para la división de desarrollo del taller. Las secuencias del programa de control del CNC se visualizan directamente y en tiempo real. Se puede obtener una presentación en 3D a la medida del cliente de acuerdo con las distintas configuraciones de máquina, funciones y necesidades específicas. También se pueden diseñar cursos de entrenamiento para acelerar el proceso de desarrollo. El StuderVirtual provee datos que en el pasado eran disponibles tan sólo después de hacer pruebas sobre un prototipo.
Presentación del Surfcam 2003
Surfware presentará
el último gran lanzamiento del Surfcam CAD/CAM Systems. En EMO, los visitantes
podrán apreciar demostraciones del Surfcam 2003 que incluye varias novedades.
Es el caso de la asociatividad completa a través de su software para
manufactura. Esto incluye sus productos para mecanizado de 2 a 5 ejes, máquinas
rotatorias y electroerosionadoras, donde los parámetros de mecanizado
se asocian con la geometría. Cuando ocurren cambios en la geometría
de la pieza, en la herramienta o en los parámetros de corte, el sistema
puede fácil y eficientemente regenerar el recorrido de la herramienta.
La asociatividad de Surfcam se extiende a través de todo el sistema, aun hasta su tecnología para el procesamiento de agujeros. La función de mover un agujero después que el sistema ha creado el recorrido de la herramienta es aún más fácil, ya que le permite al usuario regenerar el recorrido para la nueva posición del agujero. También está asociado con modelos sólidos importados de Surfcam Solids o Solidworks. El sistema reconoce los cambios hechos sobre el modelo sólido, advierte automáticamente al usuario que el modelo ha sido cambiado y suministra distintas opciones para regeneración.
Otra de las novedades es el Surfcam 3D Offset Finishing, que calcula el recorrido de la herramienta con base en la superficie de la pieza, para que los pases de la herramienta sean paralelos a la pieza y produzcan un recorrido más uniforme. Esto se refleja en una altura de pico constante y un acabado más fino a lo largo de todo el modelo, que al final requiere menos pulido. Este proceso también reduce el tiempo de ciclo total, ya que las cargas del corte de viruta son consistentes y, por lo tanto, la velocidad de corte y avance se pueden incrementar ampliamente.
El Flat Surface Finishing identifica automáticamente las superficies planas en un modelo y genera el recorrido de la herramienta que remueve completamente cualquier pico remanente de una operación de acabado anterior. Esto reduce significativamente o puede aun eliminar la necesidad de pulido manual en estas áreas.
Para el fresado de chaflanes, Surfcam creó una operación dedicada que utiliza herramientas específicas de chaflanado a fin de generar los recorridos de la herramienta y así eliminar los bordes exteriores afilados de un modelo después que ha sido completamente mecanizado. Por lo general, las piezas de alta precisión requieren un corte de borde dentro de cierta tolerancia. Hacer esto manualmente reduce el control sobre la consistencia y calidad de la pieza. Si se tiene una operación dedicada para este objetivo, se reduce el tiempo de programación y se crean recorridos de herramienta más eficientes para este tipo de herramienta.
Nuevas soluciones de programación CAM
Certificado por Microsoft
como ´diseñado para Windows XP´, el GibbsCAM 2004 presenta
una nueva interfaz de usuario y numerosas mejoras, posibles gracias a su ambiente
Windows. Además de la apariencia de los elementos de control tipo XP,
el programa ofrece capacidades más potentes como la función ‘corte
y pegue’, que permite la transferencia de datos entre sesiones concurrentes
de GibbsCAM.
La nueva función Hole Manager, una de las mejoras de esta versión, que ahorra tiempo de trabajo, proporciona una interfaz que agrupa huecos para su manipulación y procesamiento. De esta manera, cada grupo de huecos puede ser programado automáticamente con Hole Wizard, una función basada en el conocimiento de la experiencia codificada del usuario. Sin embargo, en todo momento el usuario tiene control total para modificar las recomendaciones dadas por el sistema.
Para asegurar que los usuarios puedan leer y mecanizar datos de CAD de cualquier fuente, las capacidades GibbsCAM para intercambio de datos han sido expandidas con la incorporación de soporte nativo para CATIA V5, PTC Wildfire, Inventor y AutoCAD 2004 de Autodesk, ACIS V10 y Parasolid V15. El GibbsCAM 2004, certificado para Inventor 7 y Solid Edge V14, es compatible con SolidWorks 2004.
La nueva opción 2.5D Solids fue diseñada específicamente para suministrar a los usuarios que mecanicen sólidos 2.5D una función de programación CNC destinada al mecanizado de producción. GibbsCAM ha sido mejorado para interactuar con piezas 2.5D, mediante la adición de una función interactiva y con herramientas de selección de caras para reconocer los rasgos de mecanizado de la geometría 2.5D.
La opción 2.5D también incluye una función avanzada de reconocimiento automático de rasgos (AFR, Automatic Feature Recognition), que identifica los huecos en modelos sólidos. Una vez reconocidos por la AFR, los datos de los huecos y sus parámetros son cargados en el Hole Manager para su programación automática. La tecnología de sólidos también fue utilizada para mejorar la función de contorneado de GibbsCAM, proporcionándole, donde fuera posible, el análisis de caminos de la herramienta con poliarcos, en lugar de utilizar polilíneas.
Nuevo sistema portabrocas
Seco Tools ha presentado
en el mercado un nuevo y competitivo sistema de sujeción de brocas, que
cubre un amplio rango de opciones, entre brocas de carburo sólido, brocas
de insertos soldados y el sistema CrownLoc, de Seco.
El rango de opciones de portabrocas incluye inductores de refrigerante para cambio manual y automático de herramientas, con un total de seis diferentes inductores para dos velocidades máximas de trabajo recomendadas (4.000 rpm y 6.000 rpm). El nivel límite de presión es de 290 psi. Adicionalmente, se encuentran disponibles nuevos portaherramientas para brocas de insertos ajustables, con una exactitud de ± 0,002" (± 0,05 mm). Estos portaherramientas vienen con o sin inductores de refrigerante. El nuevo sistema de portabrocas para todos los estilos es de diseño modular y cuenta con extremo posterior Graflex.
Adicionalmente, Seco-Carboloy ha publicado una nueva hoja de datos que contiene información sobre sus nuevas brocas de carburo sólido con geometría T, diseñadas especialmente para el mecanizado de titanio y de aleaciones de titanio. Las hojas presentan una figura a todo color de la nueva broca y un análisis acerca de los beneficios y funciones de la geometría. También incluyen tablas de maquinabilidad y datos de corte.
La nueva broca cuenta con bordes agudos de corte, un cono posterior largo y geometría optimizada. Estas características reducen la deformación de la pieza de trabajo, la excesiva generación de calor, los esfuerzos residuales en la superficie de los huecos y la creación de rebabas de salida. Otros beneficios adicionales de la nueva geometría T incluyen mayor vida de la herramienta, productividad superior, menor endurecimiento por trabajado y calidad mejorada de los huecos.
Centro de trabajo láser
El Centro de trabajo láser
FPL-6 de Finn-Power es un sofisticado sistema de corte por láser de alta
producción para fabricación en lámina que proporciona mayor
velocidad, exactitud y alta calidad de piezas. Ha sido diseñado con la
nueva tecnología de motores lineales que le permite desarrollar altas
velocidades, incluso en pequeños orificios y en contornos estrechos.
El FPL-6 procesa piezas hasta de 1.500 mm (60") x 3.000 mm (120"), en varios tipos de material y de espesores. Aceros blandos hasta de 20 mm (0,78"), aceros inoxidables hasta de 12 mm (0,47") y aluminio hasta de 8 mm (0,32"). Su sistema de óptica móvil tiene una velocidad de posicionamiento hasta de 300 m/min (11.811"/min) en los ejes X y Y. El máximo peso de la pieza de trabajo es de 800 kg (1.760 lb) y tiene una tolerancia de repetición de ± 0,025 mm (± 0,0001") con una velocidad de contorneado hasta de 20 m/min (787"/min) con corte asistido por nitrógeno en aceros blandos de 1 mm de espesor (0,039").
Para minimizar el tiempo de alistamiento durante el cambio de foco del lente, se ha diseñado un nuevo cabezal de corte de alta presión integrado al sistema. La distancia constante entre la superficie del material y la boquilla es asegurada con una unidad sensora integrada de registro de capacidad. El cabezal de corte no se tiene que cambiar cuando se requiere un cambio de distancia focal. Sólo debe ser insertado, en unos segundos, un nuevo cartucho de lente. Hay cartuchos disponibles para distancias focales de 5" y 7,5".
El FPL-6 proporciona grandes ventajas al incrementar la velocidad de procesamiento, en especial con la nueva función de posicionamiento Ping-Pong, desarrollada para lograr transiciones suaves y eficientes que aumentan la productividad.
Otras funciones incluyen el sistema de rayo láser con sólo dos espejos externos, aceleraciones en los ejes X y Y mayores de 2 g, adaptador de modo intercambiable para obtener máximo desempeño en cualquier condición y un sistema de mesa que permite procesamiento y posicionamiento continuos de las piezas con acceso desde tres lados.
Nueva celda de manufactura
flexible para punzonado, conformado y corte por láser
La nueva celda flexible
de manufactura (FMC, Flexible Manufacturing Cell) LPE, de Finn-Power, combina
una prensa de punzonado E5 de torreta de seis ejes, comandada por servomotores,
la última generación de láser CO2, y un robot para carga
automática, descarga y apilamiento. La celda LPE permite el punzonado,
marcado, roscado, ranurado, resaltado, doblado y corte por láser en una
sola máquina.
Ha sido diseñada para aplicaciones de precisión. Mediante un solo alistamiento, el material de inventario puede ser convertido en piezas finales sin ninguna manipulación adicional. El uso óptimo de la LPE permite utilizar la prensa de punzonado cuando sea más fácil o rápida y el láser cuando sea más efectivo. Los usuarios tienen la opción de analizar las piezas, los materiales, las particularidades y el tiempo y costo total de las piezas para determinar el mejor proceso de producción de cada proyecto.
Una vez el material entra al sistema, la LPE produce una pieza terminada. Esta innovación en la industria suministra un sistema que combina herramientas de doblado con un cabezal de corte por láser en una prensa de torreta (que aumenta la creatividad y la flexibilidad en la manufactura de piezas). El resaltado es una función de la LPE que proporciona un proceso exacto para bloqueos, topes y resaltos en general. Finn-Power resolvió el problema convencional de la altura del dado que impide el movimiento libre de la lámina. El novedoso diseño admite el conformado de resaltos hasta de 0,62" (16 mm), mediante un dado que se mueve hacia arriba y luego se retrae, permitiendo el movimiento libre de la lámina.
El robot de carga, apilado y descarga (LSR) alimenta con láminas la punzonadora de torreta y apila las piezas terminadas en pallets especiales. Tiene la capacidad de manipular una gran variedad de piezas, que puede tomar cerca del cabezal luego del conformado y, posteriormente, colocarlas en posiciones precisas en sitios especiales para piezas terminadas.
Mecanizado flexible
Buffoli, proveedor de máquinas
CNC de barra rotatoria y no rotatoria, ofrece una alternativa a los problemas
de rentabilidad de los sistemas automáticos multihusillo, ocasionados
por demoras en los cambios de herramienta, poca flexibilidad y altos costos
de operaciones secundarias en piezas complejas. Su nueva máquina flexible
universal CNC Trans-Bar 55+, brinda alta productividad para mecanizado completo
de piezas de barra no rotatoria (con capacidad para barra de 55 milímetros).
También mostrará, por medio de equipos multimedia, el nuevo centro
de mecanizado de 2 x 5 ejes Omni-Flex ´Quattro´. Este centro de mecanizado
de dos plataformas tiene la capacidad de mecanizar piezas por sus seis lados
y en cualquier orientación angular. La máquina está equipada
con dos volantes, cada uno con CNC completo para posicionamiento rotacional,
80 herramientas en cuatro magazines (de 20 herramientas cada uno) y cuatro motores
de 25 kw (12.000 rpm) para complementar velocidad y flexibilidad de los husillos.
Las máquinas Trans-Bar 55+ están diseñadas para compañías de mecanizado que trabajan por subcontrato y que buscan una máxima flexibilidad y convertibilidad en ciclos de corta duración. Además de este atributo, las Trans-Bar 55+ son máquinas de alta eficiencia, con gran capacidad de procesamiento sin intervención humana, lo que permite una operación automática durante todo el ciclo de trabajo. El proceso de barra no rotatoria, que también mejora muchos aspectos relacionados con la calidad de la pieza, mantiene siempre tolerancias y relaciones precisas entre las características radiales y el acabado, garantizando al mismo tiempo la concentricidad en operaciones de mecanizado interno y externo. Cuarenta herramientas permiten el mecanizado de piezas de precisión en su parte frontal y posterior, así como en todas sus superficies externas e internas y una amplia variedad de formas transversales.
El CNC y unidades de tres ejes, que permiten el uso de insertos estándares de bajo costo para mecanizado de contornos por interpolación, incluido el roscado de un solo punto y el fresado poligonal, minimizan los costos de herramental y de mano de obra por pieza producida. El cambio de herramental toma de 30 a 90 minutos y facilita la producción en baja cuantía. Los tiempos de ciclo son normalmente 50% más cortos que los de una máquina automática multihusillo, más favorables en economías de escala para producción en masa. Incluso las piezas más complejas pueden ser terminadas tanto en las dos direcciones como transversalmente, en un solo alistamiento. En promedio, estas máquinas generan tiempos de ciclos de 2 a 10 segundos.
Mecanizado para moldes y herramientas
Hermle exhibirá
la nueva máquina Universal U 740, con diseño de bloque sólido,
soporte de tres puntos y tecnología de fundición de mineral.
La U 740 es un concepto de máquina que se ha probado con nuevos alcances tecnológicos, ideal para la fabricación de moldes y herramientas y la producción de piezas únicas y en pequeñas series.
Existe en diseños de tres, cuatro y cinco ejes. Realiza mecanizado simultáneo por los cinco lados o con cinco ejes, como con el control CNC del eje B, mesa rotatoria NC, cambiador de herramientas y opciones individuales.
El mecanizado con cuatro ejes es posible con una mesa rígidamente enclavada, cabeza rotatoria NC, husillo principal con rotación manual y display digital, intercambiador de herramientas y opciones individuales.
El mecanizado con tres ejes se realiza con mesa rígidamente enclavada, husillo principal rígido y opciones individuales. Convencionalmente, el eje de rotación de los husillos principales rotatorios se encuentra exactamente en su centro de rotación, de forma que cuando el husillo cambia de posición vertical a posición transversal (horizontal), la mitad de su ancho queda fuera de la superficie de enclavamiento de la mesa y requiere el uso de una placa de soporte bajo las piezas planas.
Hermle ha colocado el centro del husillo fuera de su centro de rotación. De esta forma, el husillo queda cerca de la superficie de enclavamiento de la mesa cuando se mueve a su posición transversal. Así, la tediosa operación de colocar soportes bajo las piezas se reduce sustancialmente.
Entre las características de la U 740 están el diseño de bloque sólido con tres puntos de soporte y su tecnología de fundición de mineral; el eje B con control CNC y rotación entre +5°/-95° con encajado hidráulico; husillo principal de rotación manual entre +5°/-95° con display digital sobre la unidad de control; velocidad desde 12.000 hasta un máximo de 18.000 rpm y un torque de 200 Nm; amplio desplazamiento en X de 740/915 mm; desplazamientos rápidos hasta de 30 m/min; aceleraciones hasta de 4 m/s2; carga máxima de la mesa de hasta 700 kg; área de trabajo completamente aislada; panel de control con rotación desde la posición de trabajo hasta el punto de carga y descarga de la herramienta; diseño modular que incluye opciones de extensión, y avanzada tecnología de control con el iTNC 530.
Rectificado para
diversas aplicaciones
Junker presentará
la rectificadora EJ 29 silver, multifuncional OD e ID, para manufactura de piezas
únicas y pequeños lotes. Esta máquina cubre un amplio rango
de aplicaciones de rectificado para empresas pequeñas y medianas que
trabajan por subcontrato, así como para fabricantes de herramientas y
máquinas. Se caracteriza por su flexibilidad y precisión.
También resulta especialmente adecuada para aplicaciones complejas que requieren un alto grado de elaboración. La máquina se encuentra disponible con una cubierta completa de protección o con un protector impermeable abierto, según las necesidades del usuario. El diseño de esta máquina con accesibilidad mejorada y estructura más transparente, así como su desempeño en el rectificado, rivaliza con los mejores competidores del mercado. Un sistema de control CNC moderno y flexible, Fanuc 21i, asegura la máxima eficiencia incluso con personal sin capacitación. Entre otras características, ofrece manejadores digitales de gran escala y un sistema de medición absoluta de alta precisión en todos los ejes CNC. Los volantes de mando electrónico independientes para los ejes X y Z le permiten al operario operaciones de rectificado manual.
Además de sus altos estándares en ergonomía y diseño moderno, de acuerdo con las normas de seguridad de la CE, la EJ 29 silver proporciona un amplio rango de equipos especiales sin costo adicional, que incluyen dispositivos para rectificado de interiores, modernos programas de preparación, escala de nivel en el eje X, sistema hidráulico para manejo de colas y muchos equipos más.
Junker también tiene un concepto de servicio al cliente. Cada cliente tiene un asesor de servicio personalizado, que se encarga de arrancar la máquina y de entrenar al personal. Esta persona de contacto directo se encuentra disponible para responder cualquier pregunta.
Manguitos de potencia
de Röhm
Röhm presentará
las mordazas con dientes rectos que cuentan con un sistema de cambio de mordazas
de acción rápida con desenganche individual de cada mordaza y
aseguramiento de la posición de las mordazas base. El diseño especial,
con un arreglo tangencial de barras cónicas, tiene un efecto positivo
sobre el comportamiento de la fuerza centrífuga de este manguito. Esto
significa menores pérdidas con la fuerza centrífuga y mayores
revoluciones por minuto (con mayor salida). El seguro de posición de
la mordaza base garantiza un agarre completo de la barra de calce con la mordaza
base. El arreglo de aseguramiento individual significa que el manejo es particularmente
fácil con bloques mordaza especialmente largos cuando la pieza los requiere.
Röhm también exhibirá los cilindros hidráulicos sin agujero pasante, con sensores de posición magneto-restrictivos, que utilizan diferentes efectos mecánicos para monitorear la longitud de la carrera. Este tipo de sensores de posición es suministrado con terminal análoga, digital o bus de campo.
Delcam presentará su nuevo software PowerMILL CAM en EMO
El objetivo principal del stand de Delcam en EMO Milán será la presentación de la última versión del software de CAM PowerMILL. El PowerMILL 5 ofrecerá una programación más sencilla a pesar de la incorporación de un rango de estrategias aún más amplio. Algunas de sus características principales incluyen interfaz de avanzada, nuevos elementos para automatizar la programación, mecanizado con variación de espesor, identificación más completa de colisiones y opciones de simulación. La nueva interfaz para operaciones de limpieza de superficies complementa la transición con las nuevas formas de terminado introducidas por PowerMILL 4. Las mejoras incluyen un acceso más fácil a los comandos de uso más frecuente, menos formatos y un estilo consistente en todo el programa, lo que permitirá un entrenamiento fácil y rápido para los nuevos usuarios. De las muchas opciones de mecanizado en PowerMILL 5, tal vez la más importante es el mejoramiento en las operaciones de desbaste. Para esto se utiliza una técnica de inventario de modelos que disminuye en el tiempo de cálculo y una mejora la precisión durante el mecanizado. Esto asegura una máxima cantidad de remoción de material con cada herramienta. Los beneficios serán particularmente significativos cuando se utilice progresivamente una gran serie de herramientas pequeñas para mecanizar un componente.
Otra mejora importante es la habilidad de mecanizar distintas superficies de un modelo con distintos espesores de material remanente. Esta técnica se usa en la industria aerospacial en el desbaste de componentes estructurales que tienen grandes socavados con paredes delgadas. En estos casos, normalmente es recomendable desbastar las superficies planas en la base dejando un mínimo de tolerancia para disminuir las operaciones de acabado y dejar suficiente material en costillas delgadas para asegurar suficiente rigidez cuando se mecanizan con una herramienta más larga. De la misma forma, en el mecanizado de electrodos, normalmente se requiere mecanizar a la profundidad exacta en la cavidad requerida en la dirección axial y dejar al mismo tiempo una compensación negativa en la dirección radial para facilitar su conexión.
Delcam ha continuado la expansión y el mejoramiento de las estrategias disponibles para el control de cinco ejes incorporadas en el PowerMILL 4. El trabajo en proyectos de mecanizado complejo con cinco ejes le ha permitido continuar su tradición en el suministro de software para la generación de recorridos de herramienta que, además de ser matemáticamente correctos, corren eficientemente en la máquina. En el PowerMILL 5 se han introducido mejoras en la definición de la herramienta y la identificación de colisiones. El software tiene un rango más amplio de opciones para simular el portaherramienta y la capacidad de identificar las distintas áreas de la herramienta y del portaherramienta. También le permite al usuario crear un contorno límite de colisión alrededor de áreas específicas del modelo, tales como paredes escarpadas, o alrededor de abrazaderas antes de calcular cualquier recorrido de la herramienta. Esta técnica puede ser más eficiente que calcular todo el recorrido de la herramienta y luego remover y recalcular los segmentos que pueden causar alguna colisión.
Para mayor información sobre los productos y empresas mencionados, vaya a esta misma reseña, dentro de ´Showrooms y clasificados´.
Vaya al artículo central
de este informe
EMO Milán, la cita con los sistemas de producción
Te podría interesar...
Lo más leído
Reciclaje del metal duro: un negocio sostenible que reduce el impacto ambiental en la indu...
Descubre qué son los centros de mecanizado, sus funciones clave y los tipos disponibles pa...
La industria metalmecánica se encuentra en profunda transformación, conozca las tendencia...
Como parte del Open House 2023, el Grupo Hi-Tec dio a conocer ofertas tecnológicas avanzad...